Ultraschall ist unsere Stärke
Die SONOTEC GmbH ist ein führender Lösungsspezialist in der Ultraschallmesstechnik. Mit etwa 200 Mitarbeitenden entwickelt und fertigt der Hersteller am Standort Halle (Saale) kundenspezifische Ultraschallwandler und -sensoren sowie Prüfgeräte und Messtechniklösungen für die Nicht-invasive Flüssigkeitsüberwachung, Vorbeugende Instandhaltung und Zerstörungsfreie Prüfung.
Messekalender
19. Conference of the European Ceramic Society (ECerS)
European Congress of Applied Biotechnology
Single-Use Event
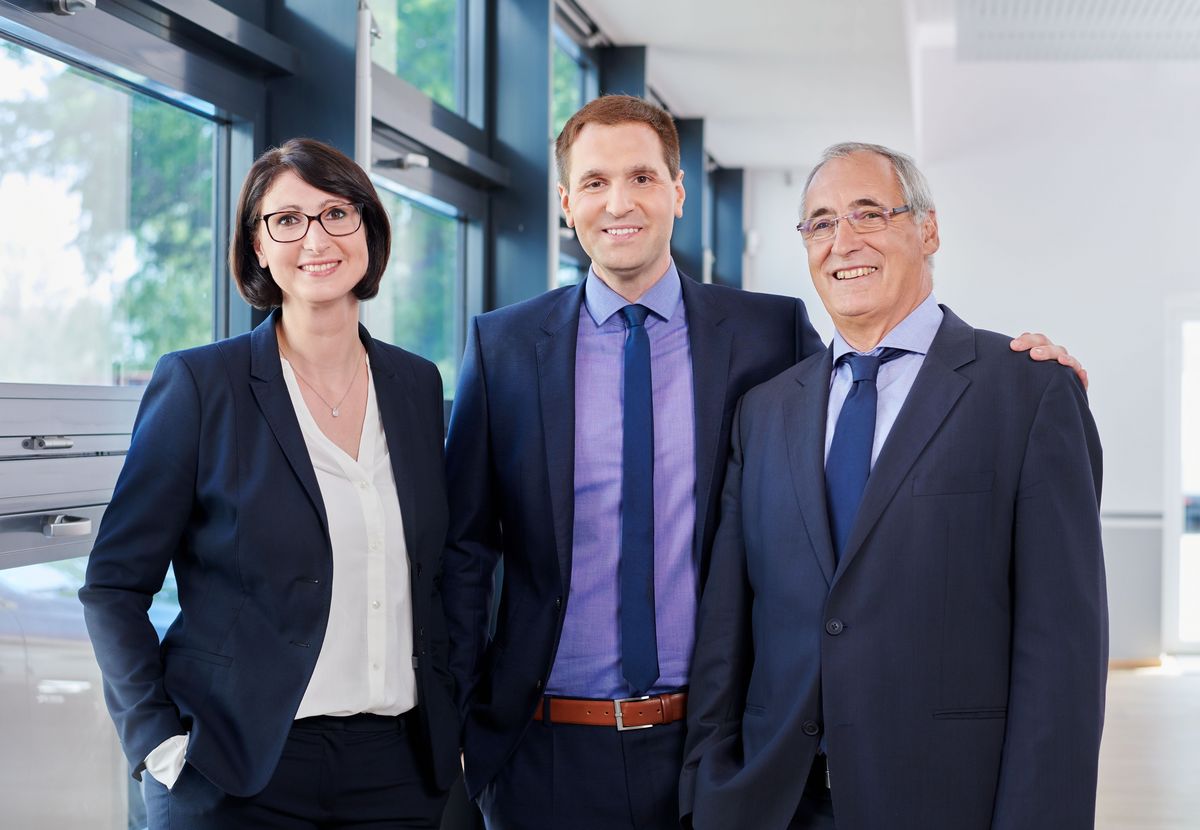
Wachstum durch Innovation mit Ultraschall
SONOTEC wurde Anfang 1991 von den Physikern Dr. Santer zur Horst- Meyer und Hans-Joachim Münch gegründet und ist seitdem inhabergeführt. Seit April 2019 verstärken Manuela und Michael Münch die Geschäftsleitung des Familienunternehmens, Dr. Santer zur Horst-Meyer steht weiterhin als Berater zur Verfügung. Mit gegenwärtig etwa 200 Mitarbeitenden sind wir ein wachsendes Technologieunternehmen, am Markt etabliert als Produkt- und Lösungsspezialist in der Ultraschallmesstechnik.
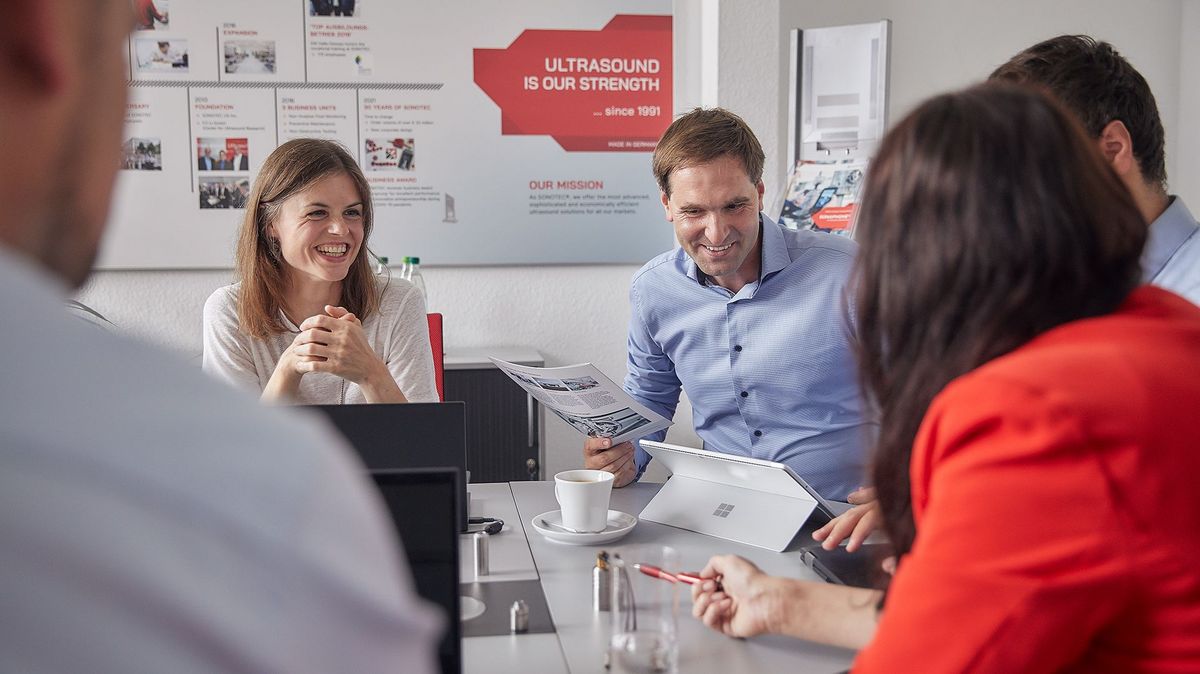
Unser Unternehmen wächst
Unser leistungsorientiertes SONOTEC-Team erweitert seine Aktivitäten im internationalen Messtechnik- und Sensormarkt. Wir suchen Mitarbeiter mit hoher Kreativität und großem Engagement. Wenn Sie an unserem Erfolg teilhaben wollen, schauen Sie sich unsere Stellenangebote an. Von Halle (Saale) aus entwickeln, produzieren und vertreiben wir internationale Spitzenlösungen der Ultraschallmesstechnik.
Wir sind zertifiziert
TÜV Rheinland zertifiziert
Management System EN ISO 13485:2016
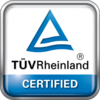
TÜV Rheinland zertifiziert
Management System ISO 9001:2015
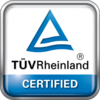
Haben Sie Fragen?
Dann kontaktieren Sie uns! Wir helfen Ihnen gerne weiter.
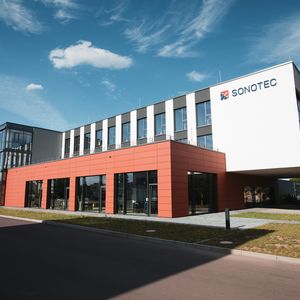
SONOTEC GmbH
Thüringer Str. 33
06112 Halle (Saale)
Deutschland