Schweißnahtprüfung mit Ultraschall
Die Schweißnahtprüfung ist eines der Hauptanwendungsgebiete der Ultraschallprüfung. Mit Hilfe von Ultraschall-Fehlersuchgeräten finden Materialprüfer Ungänzen innerhalb der Schweißnähte, die zu Material- oder Komponentenversagen führen könnten. Die Ultraschallprüfung ist ein Teil der Schweißnahtqualitätskontrolle und ist entscheidend für die Gewährleistung der Sicherheit in einem weiten Branchenumfeld, z. B. kann sie maßgeblich zur Vermeidung von Flugzeugabstürzen, Reaktorunfällen und Explosionen von Ölplattformen eingesetzt werden.
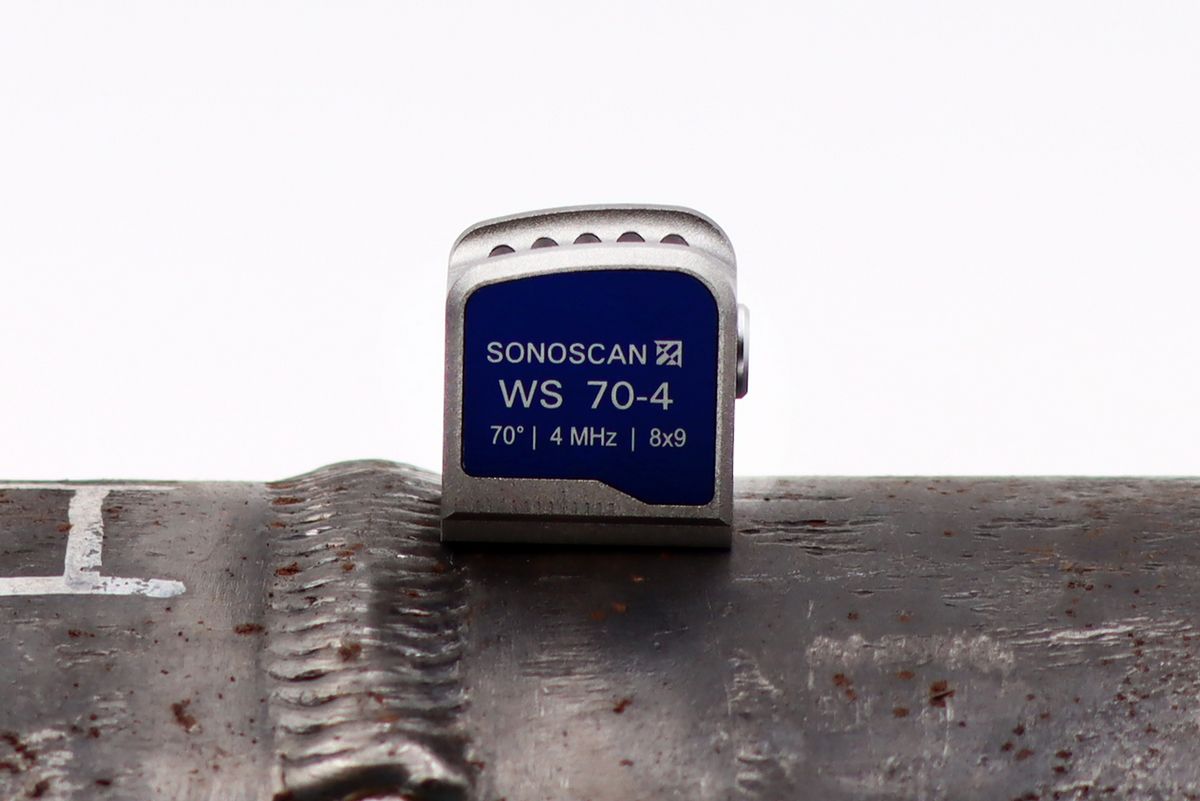
Möglichkeiten, Herausforderungen und Einschränkungen
Die Ultraschallprüfung ist ein komplexer Prozess, der qualifizierte Prüfer erfordert. Viele Faktoren müssen berücksichtigt werden bevor eine Prüfung durchgeführt werden kann, darunter:
- Physik des Ultraschalls – Wellenformen, Ausbreitung, Dämpfung, Reflexion, Modenumwandlungen etc.
- Betrieb des Prüfkopfes, Theorie und Eigenschaften – Piezoelektrischer Effekt, abgestrahltes Feld, Strahlausbreitung, Energieverlust etc.
- Gerätebedienung – Impulsgeber, Empfänger, Datendarstellung etc.
- Ultraschallprüfverfahren – Impuls-Echo, Durchschallung, Pitch-Catch etc.
- Anwendungsspezifische Anforderungen – Schweißnahtart, Form, Abmessungen, Oberflächenqualität etc.
- Gerätekalibrierung und Auswertemethoden – DAC, DGS, AWS etc.
Vorteile
- Hohe Empfindlichkeit auf Ungänzen an der Oberfläche oder nahe der Oberfläche
- Überlegene Eindringtiefe im Vergleich zu anderen ZfP-Methoden
- Bei Verwendung des Impuls-Echo-Verfahrens: einseitige Prüfung möglich
- Hohe Genauigkeit bei der Bestimmung der Position der Diskontinuität und der Abschätzung ihrer Größe und Form
- Minimale Vorbereitung des Prüfobjektes
- Digitale Geräte liefern sofortige Ergebnisse
- Dickenmessung kann zusätzlich zur Fehlersuche durchgeführt werden
Einschränkungen
- Die Oberfläche und Geometrie des Prüflings muss die Ausbreitung des Ultraschalls durch das Material ermöglichen
- Ein Kopplungsmedium ist erforderlich, um die Übertragung der Schallenergie in das Prüfobjekt zu ermöglichen
- Materialien, die rau, unregelmäßig geformt, sehr klein, außergewöhnlich dünn oder nicht homogen sind, sind schwer zu prüfen
- Mangelnde Empfindlichkeit gegenüber linearen oder parallel zum Schallfeld orientierten Fehlern
- Für die Kalibrierung der Ausrüstung und die Charakterisierung von Diskontinuitäten sind Referenznormen erforderlich
Definition der Prüfaufgabe
Es besteht kein Zweifel, dass die Ultraschallschweißnahtprüfung keine leichte Aufgabe ist. Um dies besser zu verstehen, schauen wir uns das Verfahren selbst einmal näher an:
- Welche Arten von Schweißnähten werden geprüft (Stumpfstoß, Eckstoß, Überlappstoß etc.)?
- Was ist das Objekt und wo befinden sich die Schweißnähte (Druckbehälter, Pipelines und andere Konstruktionen)?
- Wonach werden wir suchen? (Um alle Ungänzen, die entsprechend der für die Aufgabe gewählten Qualitätsstufe registriert und ausgewertet werden müssen, aufzuspüren.)
- Es ist eine Skizze anzufertigen, auf der die Lage der Schweißnähte markiert ist. Darüber hinaus sind die wichtigsten Abmessungen, Materialstärke und -typ festzuhalten.
- In welcher Produktionsphase soll der Test durchgeführt werden? (Üblicherweise wird die Prüfung nach dem Schweißen und der Wärmebehandlung und nachdem das Objekt durch eine visuelle Prüfung und eine Magnetpartikelprüfung für weitere Tests qualifiziert wurde, durchgeführt.)
- Was soll die Prüfung umfassen? Wie viele Schweißnähte sind zu prüfen? Es ist nicht immer notwendig 100% der Schweißnähte zu prüfen. Häufig werden Schwachstellen definiert, an denen die Prüfung durchgeführt wird.
- Soll das gesamte Volumen der Schweißnaht geprüft werden? In der Regel wird die Prüfung auch auf die Wärmeeinflusszone erweitert. Unter Berücksichtigung dieser Tatsache kann der maximale Abstand des Winkelprüfkopfes von der Mitte der Schweißnaht berechnet werden.
- Sobald der maximale Abstand definiert ist, muss die Prüfkopfbewegungszone auf Einschlüsse oder Delaminierungen, welche die Winkelprüfung negativ beeinflussen könnten, unter Verwendung eines SE-Senkrechtprüfkopfes geprüft werden. Wenn die geschweißten Komponenten (Platten, Rohre usw.) eine Prüfbescheinigung des Herstellers besitzen, kann dieser Schritt eventuell übersprungen werden.
- Gemäß welcher Qualitätsklasse testen wir? Dies hat den größten Einfluss auf die Bewertung von Indikationen in der Schweißnaht. Je höher die Qualitätsklasse, desto kleiner sind die Fehler, die registriert und ausgewertet werden müssen.
- Welche Bewertungsmethode wird verwendet? In der Industrie gibt es drei grundlegende Bewertungsmethoden: AVG, DAC und AWS.
Typische Fehler
Es gibt unterschiedliche Arten von Diskontinuitäten:
- Punktindikationen
- Große Indikationen
- Längsschnittindikationen
- Transversale Indikationen








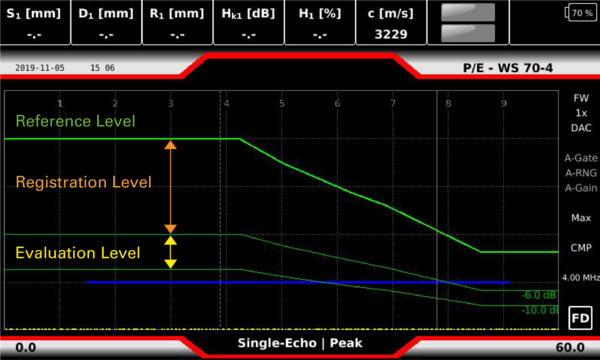
1. Die Bewertungsmethode und die Referenzschwelle für jeden in der Prüfung verwendeten Prüfkopftyp müssen definiert werden. Diese Auswahl steht in engem Zusammenhang mit der Qualitätsklasse.
- Beispiel: Eine DAC-Auswertungsmethode für SE-Prüfköpfe ist erforderlich, wenn die Referenz eine 3 mm Flachbodenbohrung ist und für Winkelprüfköpfe die DAC-Auswertung mit einer 3 mm Seitenbohrung.
2. Der nächste Schritt ist die Definition der Registrierungsschwelle. Oberhalb dieser Grenze müssen alle Indikationen registriert und im normalen Prüfprotokoll ausgewertet werden.
- Beispiel für Winkelprüfköpfe: Alle Indikationen, bei denen die Amplitude höher als -6dB von der Referenz-DAC-Kurve eines 3 mm-Seitenbohrlochs ist, müssen registriert und ausgewertet werden. Indikationen unterhalb dieses Niveaus werden nicht erfasst.
3. Zusätzlich zur Registrierungsschwelle ist die Bewertungsschwelle zu definieren. Das ist die Grenze, über der alle Indikationen bewertet, aber nicht unbedingt erfasst werden müssen. Die Bewertung dieser Indikationen führt häufig dazu, dass sie zu klein sind, um in den Bericht aufgenommen zu werden. Oberhalb der Bewertungsschwelle muss der Prüfer darauf achten, die Amplitude zu bewerten, und muss sicherstellen, dass sie die Registrierungssschwelle nicht überschreitet.
- Beispiel für Winkelprüfköpfe: Alle Indikationen, bei denen die Amplitude größer als -10dB der Referenz-DAC-Kurve einer 3 mm Seitenbohrung ist, müssen ausgewertet werden.
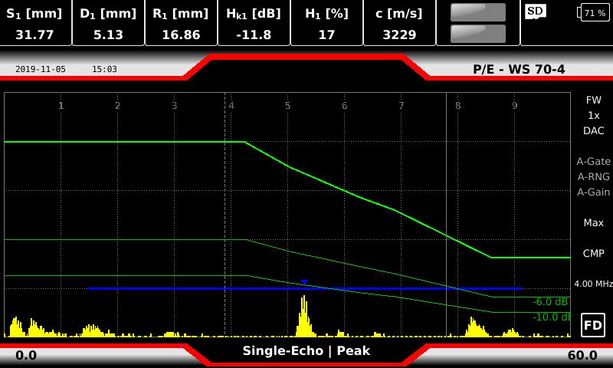
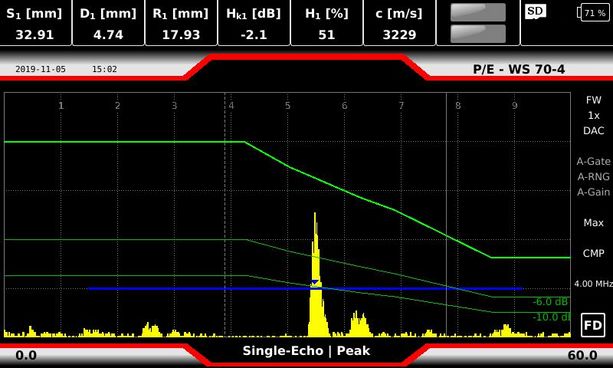
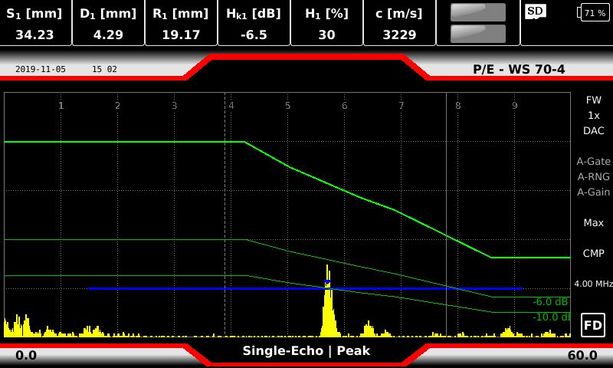
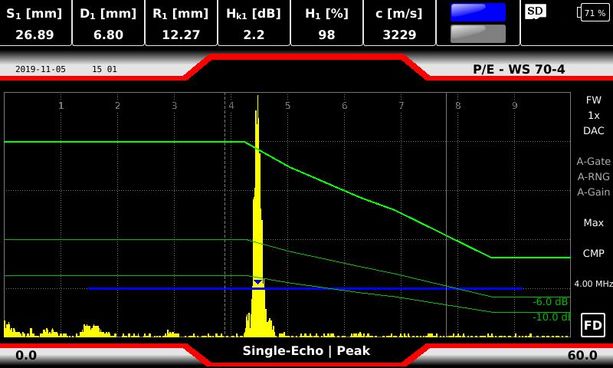
Prüfausrüstung
Ultraschallprüfgerät
Es ist ein Ultraschallprüfgerät (z. B. SONOSCREEN ST10 oder SONOWALL 70) erforderlich. Das Gerät sollte in der Lage sein, Ultraschallimpulse zu senden und zu empfangen und diese in grafischer Form darzustellen (A-Bild). Winkelprüfköpfe, automatisierte trigonometrische Berechnungen und AVG-, DAC- oder AWS-Software sind das Minimum für die Schweißnahtprüfung. Es ist entscheidend, dass die Ausrüstung in Übereinstimmung mit der Norm EN-12668-1 kalibriert und hergestellt wurde. In den meisten Branchen, in denen offizielle Schweißnahtprüfungen durchgeführt werden, müssen die Geräte mindestens einmal jährlich nach diesem Standard kalibriert werden.
Ultraschallprüfköpfe
Zweielemente-Senkrechtprüfköpfe (z. B. TS- und TL-Serie), Winkelprüfköpfe (z. B. WS-, WM- und WL-Serie) – Die Prüfkopfauswahl hängt stark vom Material ab, welches geprüft werden soll; die Geometrie, die Dicke, die minimale gesuchte Fehlergröße und viele weitere Faktoren müssen berücksichtigt werden. Um den Prüfkopfauswahlprozess zu vereinfachen, ist eine Faustregel 4 MHz-Prüfköpfe für Dicken von 8 - 50 mm und 2 MHz über 50 mm Materialdicke zu verwenden. Für eine ordnungsgemäße Prüfung müssen zwei Winkel verwendet werden. Für dünnere Schweißnähte bis zu 20 mm werden Winkel von 60° und 70° empfohlen. Für dickere Objekte werden 45° und 60° bevorzugt.
Skizze der Prüfung
Der nächste Schritt ist die Erstellung der Prüfskizze. Diese sollte die Prüfkopfbewegungszone, den Teil der Schweißnaht, der von der Prüfung abgedeckt wird, und den Punkt, an dem der Ultraschallstrahl in das Prüfobjekt eingebracht wird, deutlich darstellen. Auf dem Prüfobjekt sollte der Nullpunkt der Messung dauerhaft gesetzt und auf der Skizze markiert werden. Es muss möglich sein, die Prüfung auf Basis des Prüfberichts nach deren Abschluss exakt zu reproduzieren.
Koppelmittel
In der Regel handelt es sich dabei um ein Gel auf Wasserbasis, Öl, Fett oder Tapetenkleister. Es ist entscheidend, dass während des gesamten Prüfungsprozesses (d. h. Kalibrierung, Verlustabschätzung, Empfindlichkeitsjustierung und Prüfung) das gleiche Koppelmittel verwendet wird.
Durchführung der Ultraschallprüfung
Vorbereitung der Oberfläche
Zu Beginn muss eine Sichtprüfung der Schweißnaht und des sie umgebenden Materials durchgeführt werden um sicherzustellen, dass die Oberfläche für eine Ultraschallprüfung geeignet ist. Es können Schweißspritzer oder andere Hindernisse, die die Bewegung der Sonde einschränken auftreten; diese müssen vor Beginn der Prüfung entfernt werden. Darüber hinaus sollte die Nahtgeometrie auf mögliche Wurzeldurchbrüche oder Decklagenüberlappungen untersucht werden, da diese Indikationen aufgrund der Geometrie zeigen.
Vorbereitung der Ausrüstung
- Vor der Prüfung mit Winkelprüfköpfen müssen das X-Maß (Ausrittspunkt des Schalls) und der tatsächliche Brechungswinkel bestimmt werden. Das X-Maß ist der Punkt, an dem die Mitte des Schallfeldes aus dem Vorlauf der Sonde austritt. Dieser Punkt ist ein Nullpunkt für alle trigonometrischen Abstands- und Tiefenmessungen. Er kann unter Verwendung des Kalibrierblocks K1 oder K2 bestimmt werden.
- Die Überprüfung des Prüfkopfwinkels ist für die korrekte Berechnung von Entfernungen und Tiefen wichtig und kann ebenfalls mit dem K1 oder K2 Kalibrierblock bestimmt werden.
- Der nächste Schritt ist die Durchführung einer Entfernungskalibrierung. Dieser Vorgang wird durch die Prüfkopfauswahl beeinflusst und kann am K1 oder K2 Kalibrierblock erledigt werden. Um eine ordnungsgemäße Kalibrierung zu gewährleisten, muss die Dicke des Kalibrierblockes größer sein, als der Prüfkopfdurchmesser. Die Entfernungsjustierung ist notwendig um die präzise Schallgeschwindigkeit und die Verzögerung durch den Prüfkopfvorlauf zu bestimmen. Der bevorzugte Kalibriertyp ist die 2-Punkt-Kalibrierung, bei der diese beiden Faktoren gleichzeitig berechnet werden.
- Zum Schluss muss eine Empfindlichkeitsjustierung durchgeführt werden. Dies schließt die Wahl der Bewertungsmethode ein und erzeugt eine Bewertungskurve auf dem Prüfgerätedisplay. Die DAC-Methode erfordert einen speziell angefertigten Kalibrierblock aus dem gleichen Material, üblicherweise mit Seitenbohrlöchern in unterschiedlichen Tiefen; um eine hohe Genauigkeit zu erreichen, sollte die Tiefe der Bohrungen den Bereich der aktuellen Prüfung abdecken. Die AVG und AWS-Methoden erfordern keine zusätzlichen Blöcke, da die Kurvenberechnung empirisch vorgenommen wird.
Prüfung der Schweißnaht
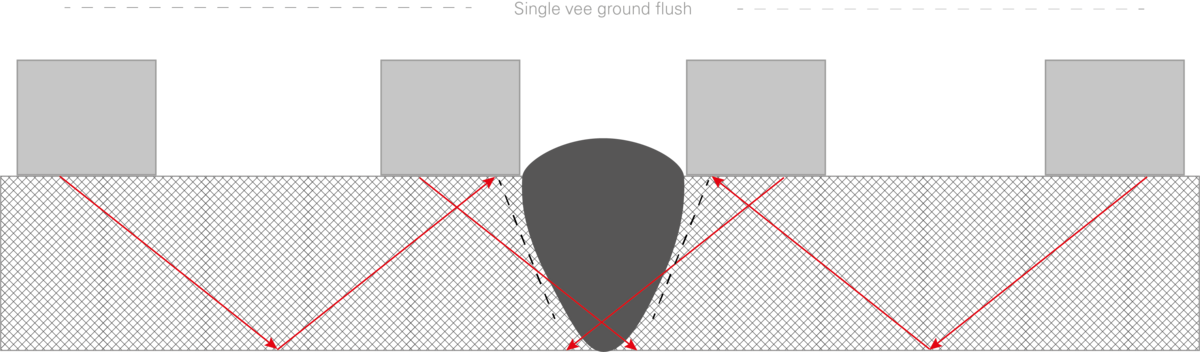
Um das Volumen der Naht zu 100 % abzudecken, muss der Winkelprüfkopf rechtwinklig zur Schweißnaht vor- und zurückbewegt werden, vorzugsweise von beiden Seiten.
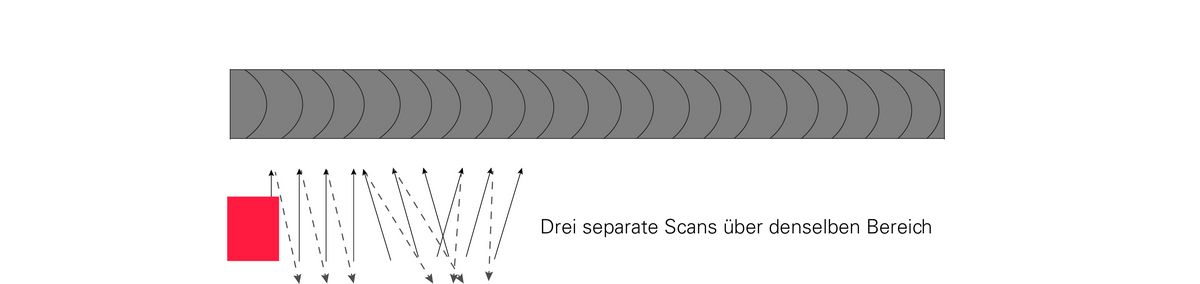
Um die Detektion schräg liegender Diskontinuitäten sicherzustellen, ist es empfohlen den Prüfkopf in einem 90° und 45° Winkel zur Nahtachse vor- und zurückzubewegen.
Klassifikation von Diskontinuitäten
Die Indikationen sollten nach ihrer Ausdehnung bewertet werden. Zuerst muss die maximale Amplitude der Indikation gefunden werden. Wenn die Amplitude stetig bis auf Null abnimmt, wenn der Prüfkopf von der Indikation wegbewegt wird, bedeutet dies, dass die Diskontinuität kleiner als das Schallfeld des Prüfkopfes ist. Wenn die Amplitude nicht bis auf Null abfällt und innerhalb eines dynamischen Bereiches von -6dB bleibt, bedeutet dies, dass die Indikation größer als die Schallfeldausdehnung ist. Fehlerhafte Indikationen können häufig auftreten: Diese sind auf Wellenumwandlungen, die durch die Objektgeometrie auftreten, zurückzuführen und müssen korrekt bewertet und ignoriert werden. Dies ist der schwierigste Teil im gesamten Prozess der Ultraschallprüfung.
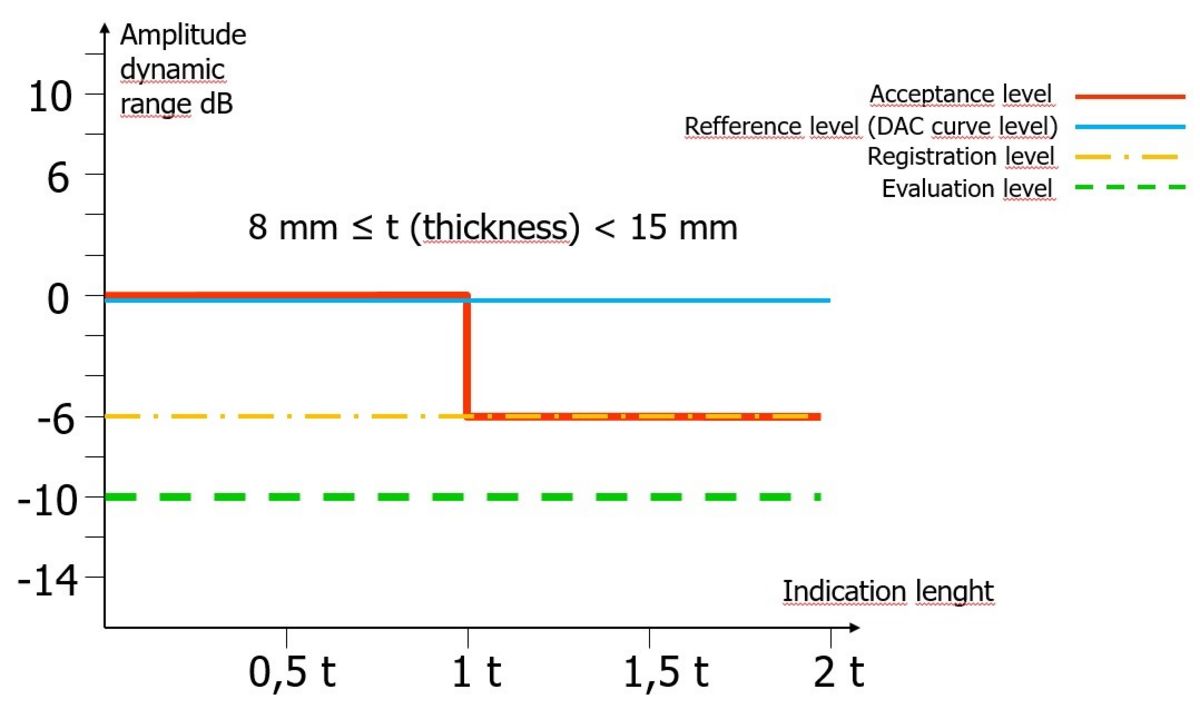
Akzeptanzkriterien: Diese sind in der Norm für jede Qualitätsklasse definiert. Zur Veranschaulichung betrachten wir das folgende Beispiel:
- Wie in der Grafik dargestellt, ist das Akzeptanzlevel gleich der Referenzschwelle (DAC-Kurvenverlauf) solange die Indikation kürzer als die Materialdicke ist. Für Indikationen, die länger als die Materialdicke sind, ist das Akzeptanzlevel 6dB unterhalb der Referenzgrenze (und gleich der Registrierungsschwelle). Dies beruht darauf, dass lange Defekte einen größeren Einfluss auf jede Konstruktion haben als punktuelle Defekte und daher mit einem niedrigeren Akzeptanzlevel bewertet werden müssen.
- Während der Prüfung müssen solche Indikationen, welche nicht akzeptiert werden, dauerhaft markiert werden.
- Vor Beendigung der Prüfung und Verlassen des Prüfortes sind das Koppelmittel und andere Rückstände der Prüfung zu entfernen.
Haben Sie Fragen?
Dann kontaktieren Sie uns! Wir helfen Ihnen gerne weiter.
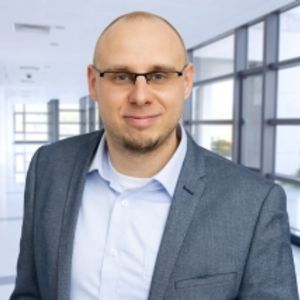